Your exclusive customer link to the digital world of tunnelling
Double Shield TBMs in operation
Double Shield TBMs are among the most technically sophisticated tunnel boring machines. They unify the functional principles of Gripper and Single Shield TBMs in one machine. Under stable geological conditions, the combination of methods allows for the installation of concrete segments parallel to tunnelling, achieving very high tunnelling performances. This powerful technology is therefore perfectly suited for excavating long tunnels in hard rock.
Advancing with power
When tunnelling with a Double Shield TBM, a rotating cutterhead equipped with disc cutters is pressed against the tunnel face with a pressure of up to 32 tonnes per disc. Due to the rolling movement of the discs, single pieces – so-called chips – are broken out of the rock. Water jets can cool the cutting tools and reduce dust formation. Buckets installed at the cutterhead take up the excavated material. Due to gravity, it slides to the center of the machine through integrated muck chutes while the cutterhead rotates and then falls through the funnel-shaped muck ring onto the machine belt. At the end of the machine belt, the rock chips are passed on to belt conveyors or transport vehicles and removed from the tunnel.
Functional principle
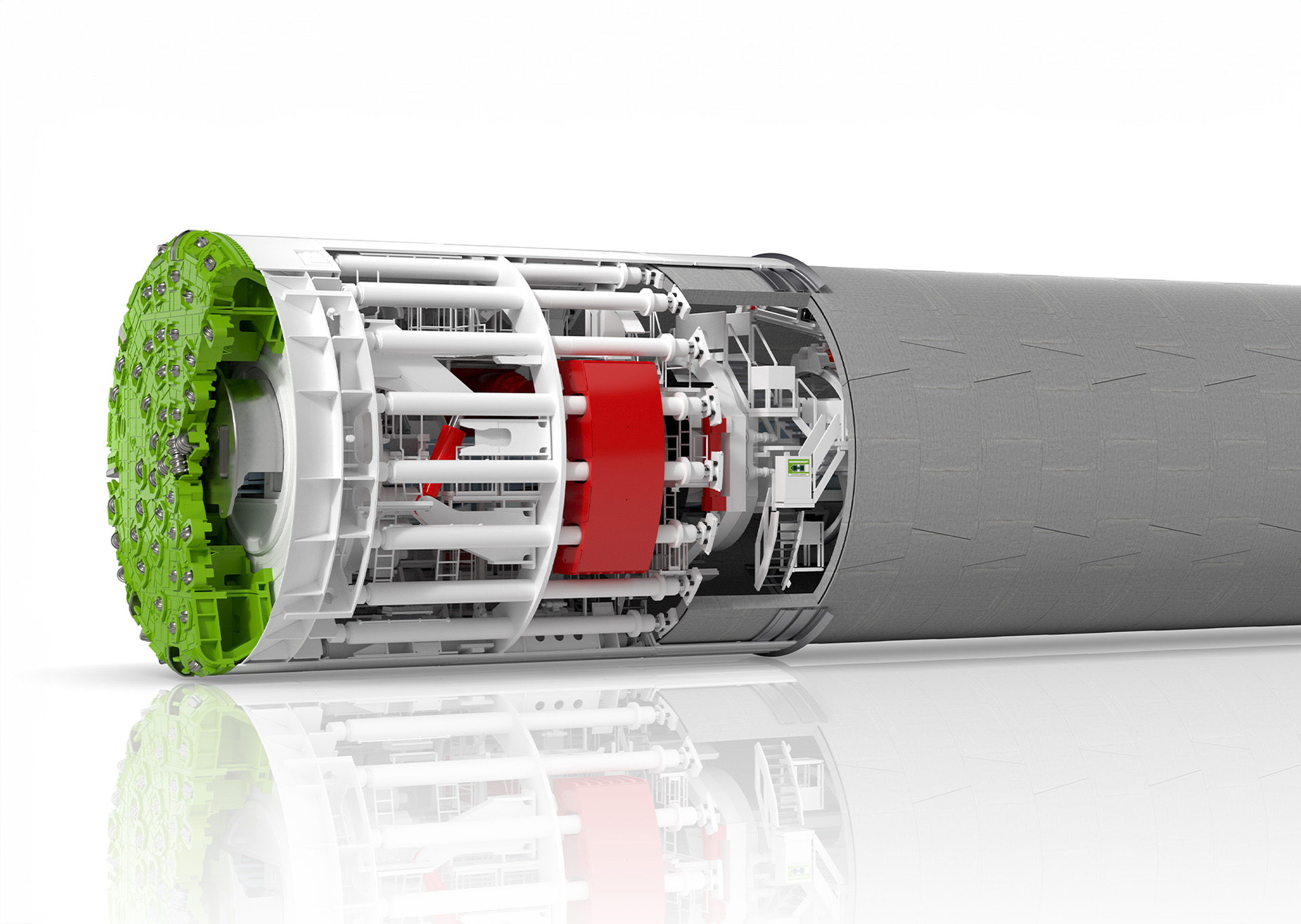
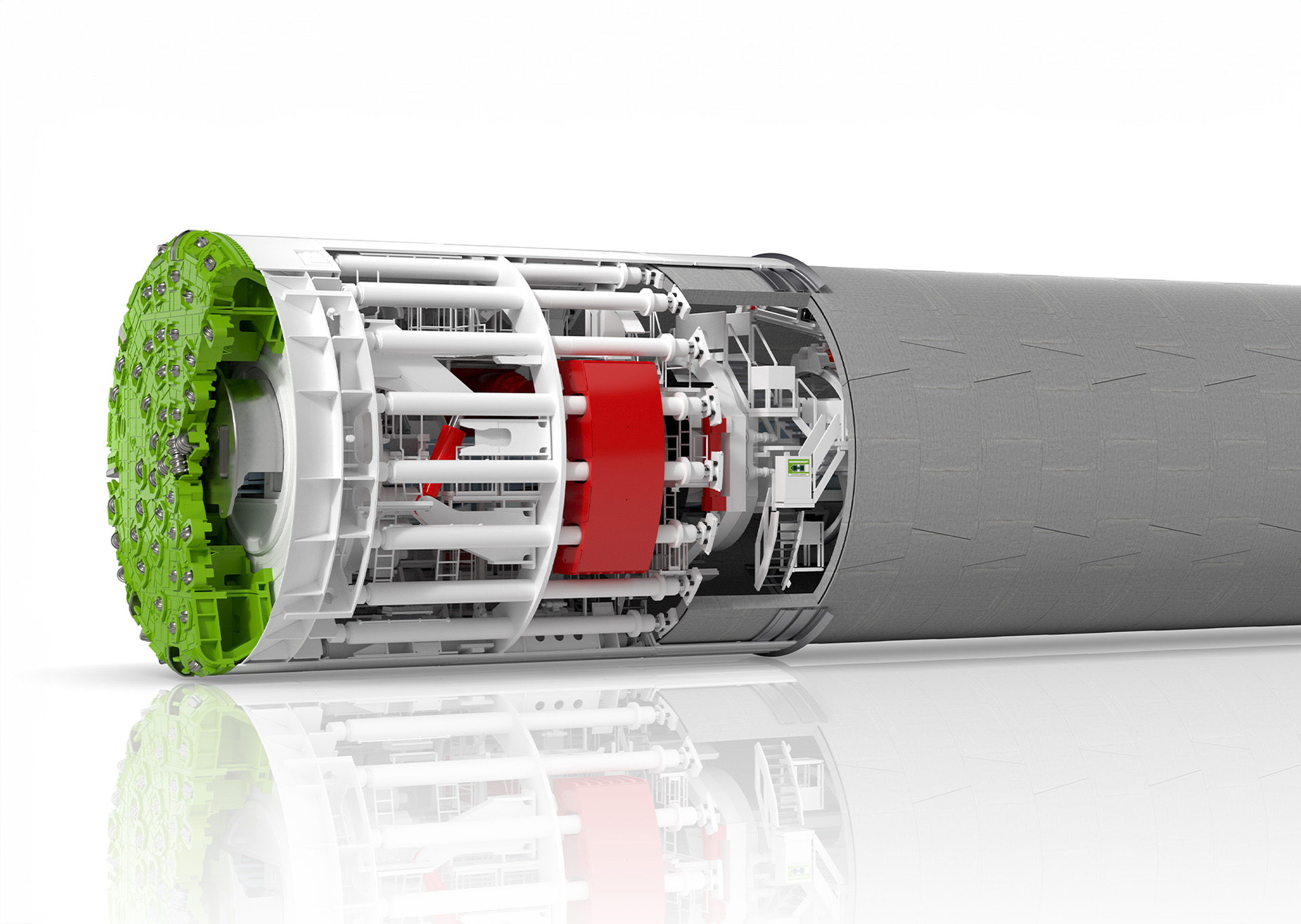
High speed due to a continuous tunnelling mode
Double Shield TBMs consist of two main components: a front shield with cutterhead, main bearing and drive, and a gripper shield with gripping unit, auxiliary thrust cylinders and tailskin. The main thrust cylinders connect the two parts of the shield. They are protected by the telescopic shield where the shield skins of the front and gripper shield overlap. Thus, Double Shield TBMs are also called telescopic shields. In stable rock, the machine is braced radially against the tunnel with the gripper shoes. This means that the front shield can be advanced independently of the gripper shield using the main thrust cylinders.
The reaction forces during the excavation process are transferred into the rock by the extended gripper shoes. Simultaneously to tunnelling, the segments are installed in the tailskin section. The auxiliary thrust cylinders serve only to secure the position of the concrete segments placed. When the stroke is completed, the gripper shoes are loosened and the gripper shield is pushed behind the front shield using the auxiliary thrust cylinders. Regripping lasts only a few minutes, which means that tunnelling is almost continuous. In ideal rock formations, Double Shield TBMs can also operate without segmental lining.
Operating principle at a glance:
Disc cutters break chips from the tunnel face applying high contact pressure
Buckets, muck chutes and muck ring provide for efficient removal of the excavated material onto a center belt conveyor
Hydraulic main thrust cylinders or auxiliary thrust cylinders push the machine forward
Segmental lining
Safe in geological fault zones
In fault zones or areas of low rock strength, radial bracing of the gripper shoes is not possible. In these sections, the telescopic shield can be retracted completely so that the front and gripper shields form a rigid unit. The necessary thrust forces are applied using the auxiliary thrust cylinders. As with the Single Shield TBM, the last segment ring installed serves as a counter bearing to advance the machine. Thrust and ring building can no longer take place simultaneously. In turn, this discontinuous mode provides for higher tunnelling safety in difficult sections of the alignment.
Application-related special solutions for difficult cases
Double Shield TBMs have a comparatively long shield skin. In cases of rock convergence there is therefore an increased risk of the machine becoming jammed. Herrenknecht engineers have developed a range of design solutions to deal with this problem. These include graded shield diameters and a vertical shift of the longitudinal axes of cutterhead, front and gripper shield, for example. Crumbling rock and excavated material can block the telescopic joint and the annular gap. This makes it difficult to push the gripper shield ahead. As a countermeasure, Herrenknecht Double Shield TBMs usually have a telescopic shield which can be moved independently. Using additional displacement cylinders, access to the tunnel wall can be provided if this is necessary for cleaning or securing measures. Additional drilling devices and drilling ports in the shield section serve to secure the open telescopic section above the TBM using a pipe arch.
The right drive for any diameter
In the diameter range from 2.8 – 6 meters, Double Shield TBMs are equipped with permanently installed drives with straight-positioned main thrust cylinders or v-positioned lattice cylinders. Tunnelling control is carried out directly by the cylinders. For diameters of more than 6 meters, movable drives with additional longitudinal displacement cylinders are generally used. Through the cylinders, the contact pressure of the drive can be measured directly, making optimum use of the power provided. An articulation bearing or torque box cylinders help control the TBM. The latter provide for continuous horizontal and vertical shift of the drive. In this way, the cutterhead can be steered precisely in all directions and can even produce a local overcut. The cutterhead can be pulled back with all drive types, allowing direct access to the tunnel face.
Meters of tunnel in continuous production
Double Shield TBMs are mainly used for tunnel projects in changing rock formations. They achieve very high tunnelling performances in stable rock by working in continuous tunnelling mode. Therefore, the combined method of Gripper and Single Shield TBM is often the quickest and most cost effective solution for long drives in hard rock.
Still got questions?
We are ready!